60. Konferencja Spawalnicza: Spawalnictwo w Dobie Przemysłu 4.0
Od wielu lat specjaliści z branży spawalniczej uczestniczą w konferencjach naukowo-technicznych, które we współpracy z Sekcją Spawalniczą SIMP naprzemiennie organizuje Instytut Spawalnictwa i ośrodki spawalnicze z całej Polski.
Konferencja odbywała się podczas Międzynarodowych Targów Spawalniczych ExpoWelding w dniach 16-18 października 2018 r. Jak zgodnie podkreślają uczestnicy, połączenie konferencji z odbywającymi się w tej samej hali targami spawalniczymi to dobre posunięcie, gdyż tematy omawiane podczas wystąpień konferencyjnych często można skonfrontować z ich praktycznym zastosowaniem, na stoiskach producentów maszyn lub materiałów spawalniczych.
Wygłoszone referaty zostały opublikowane w piątym numerze „Biuletynu Instytutu Spawalnictwa”.
Patronat honorowy nad 60. Konferencją Spawalniczą objęło Ministerstwo Przedsiębiorczości i Technologii, natomiast patronat naukowy Komitet Budowy Maszyn Polskiej Akademii Nauk.
Ponadto, przy organizacji tego wydarzenia Instytut Spawalnictwa współpracował z Instytutem Autostrada Technologii i Innowacji (IATI).
Komitet naukowy:
- prof. dr hab. inż. Jan Pilarczyk – Przewodniczący Komitetu
- prof. dr hab. inż. Janusz Adamiec
- prof. dr hab. inż. Andrzej Ambroziak
- dr hab. inż. Tomasz Chmielewski
- dr inż. Bogusław Czwórnóg
- dr hab. inż. Dariusz Golański
- prof. dr hab. inż. Stanisław Dymek
- dr hab. inż. Jacek Górka
- prof. dr hab. inż. Andrzej Klimpel
- prof. dr hab. inż. Andrzej Kolasa
- prof. dr hab. inż. Jerzy Łabanowski
- dr hab. inż. Mirosław Łomozik, prof. nzw.
- prof. dr hab. inż. Janusz Mikuła
- prof. dr. inż. Zbigniew Mirski
- prof. dr hab. inż. Jerzy Nowacki
- prof. dr hab. inż. Antoni W. Orłowicz
- dr inż. Adam Pietras
- prof. dr hab. inż. Jacek Senkara
- prof. dr hab. inż. Andrzej Skorupa
- dr hab. inż. Jacek Słania, prof. nzw.
- prof. dr hab. inż. Edmund Tasak
- dr hab. inż. Eugeniusz Turyk, prof. nzw.
- prof. dr hab. inż. Tomasz Węgrzyn
- prof. dr hab. inż. Władysław Włosiński
Relacja:
Uczestników konferencji powitali dyrektor Centrum Targowo-Konferencyjnego ExpoSilesia dr inż. Ludomir Tuszyński oraz dyrektor Instytutu Spawalnictwa, dr inż. Adam Pietras, życząc udanych wystąpień i owocnych obrad zarówno w trakcie konferencji, jak i podczas rozmów kuluarowych.
Konferencja odbywała się pod hasłem „Spawalnictwo w dobie Przemysłu 4.0”. Hasło to obecnie jest przewodnim motywem wielu konferencji i innych tego rodzaju wydarzeń nie tylko w Polsce ale i na świecie. Szereg referatów bezpośrednio nawiązywało do tej tematyki, a pozostałe ze względu na wysoki poziom merytoryczny i wykorzystanie w badaniach najnowszych technik informatycznych również wpisują się w idee Przemysłu 4.0.
W imieniu Europejskiej Federacji Spawalniczej (EWF) jej obecny prezydent p. Chris Eady z Instytutu Spawalnictwa w Anglii (The Welding Institute) omówił znaczenie zintegrowanego systemu zapewnienia jakości w rozwoju i wdrażaniu kwalifikacji zawodowych personelu spawalniczego.
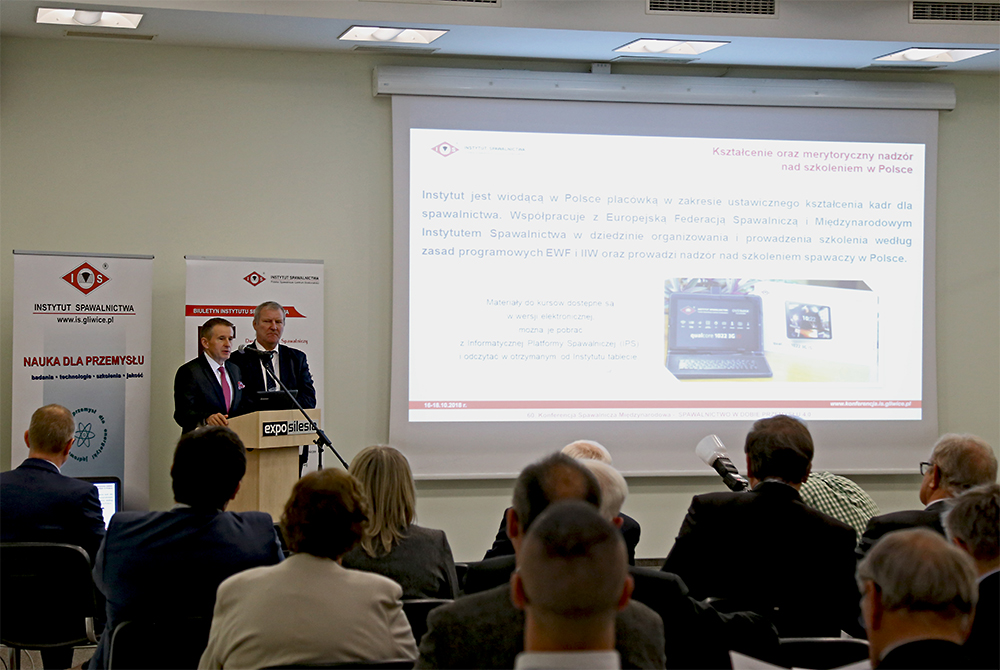
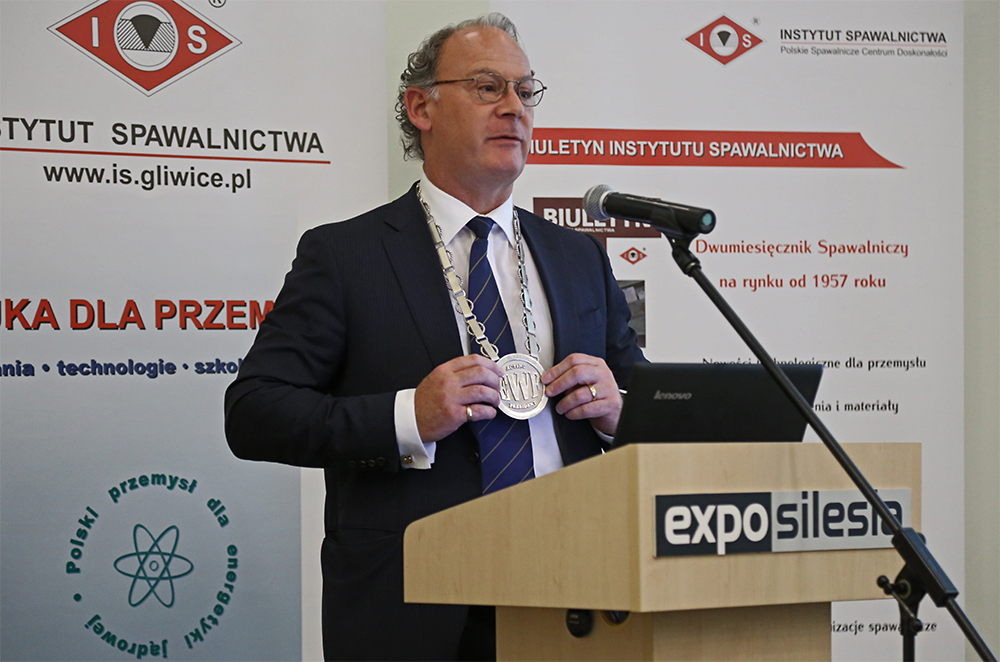
Hasło konferencji trafnie oddaje poruszaną w referatach tematykę, ponieważ autorzy przedstawiali wyniki swoich badań, z zastosowaniem najnowszych osiągnięć naukowych, nad innowacyjnymi materiałami i technologiami, jak np. robotyzacja spawania i lutospawania, spajanie współczesnych stali, zapewnienie jakości spawania, nowe techniki kontroli spoin (radiografia cyfrowa). Omawiano nowoczesne, szybko rozwijające się procesy, takie jak spawanie laserowe, spawanie wiązką elektronów, zgrzewanie z mieszaniem materiału zgrzeiny (FSW), spawanie hybrydowe i klejenie.
Wystąpienia podczas konferencji odbywały się w sześciu sesjach. Poszczególne sesje prowadzili znani przedstawiciele ośrodków spawalniczych w Polsce: prof. dr hab. inż. Andrzej Ambroziak; dr inż. Adam Pietras; prof. dr hab. inż. Jan Pilarczyk; dr hab. inż. Tomasz Chmielewski, prof. PW; prof. dr hab. inż. Andrzej Kolasa; dr hab. inż. Eugeniusz Turyk, prof. IS; dr hab. inż. Dariusz Fydrych, prof. PG; dr inż. Jolanta Matusiak; dr hab. inż. Jerzy Łabanowski i dr inż. Tomasz Pfeifer.
Program konferencji obejmował 26 referatów, z czego 10 wystąpień przygotowali autorzy z ośrodków naukowych i firm zagranicznych. Udział w konferencji wzięli przedstawiciele takich krajów, jak Niemcy, Austria, Anglia, Chiny, Czechy, Japonia, Korea Południowa Ukraina i USA. Pozostali prelegenci reprezentowali najważniejsze krajowe ośrodki spawalnicze: uczelnie techniczne i Instytut Spawalnictwa.
Oprócz wystąpień w sesjach plenarnych, uczestnicy konferencji mogli zapoznać się z wynikami badań polskich naukowców przedstawionymi w formie 10 posterów.
Oprócz wystąpień konferencyjnych miała miejsce uroczystość wręczenia Medali im. Stanisława Olszewskiego. W gronie wyróżnionych podczas tegorocznej konferencji byli: prof. Tomasz Chmielewski z Politechniki Warszawskiej oraz czterej pracownicy Instytutu Spawalnictwa – dr inż. Marek Banasik, dr inż. Tomasz Pfeifer, mgr inż. Adam Pilarczyk i dr inż. Sebastian Stano. Medale w imieniu kapituły wręczyli przewodniczący kapituły medalu prof. Zbigniew Mirski i prezes Sekcji Spawalniczej SIMP dr inż. Jan Plewniak.
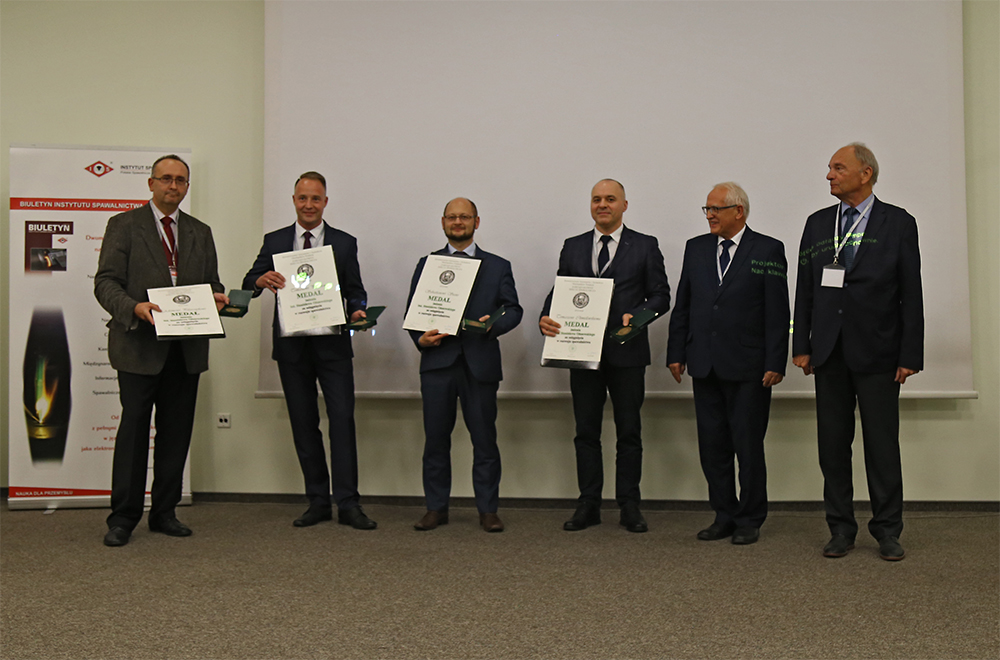
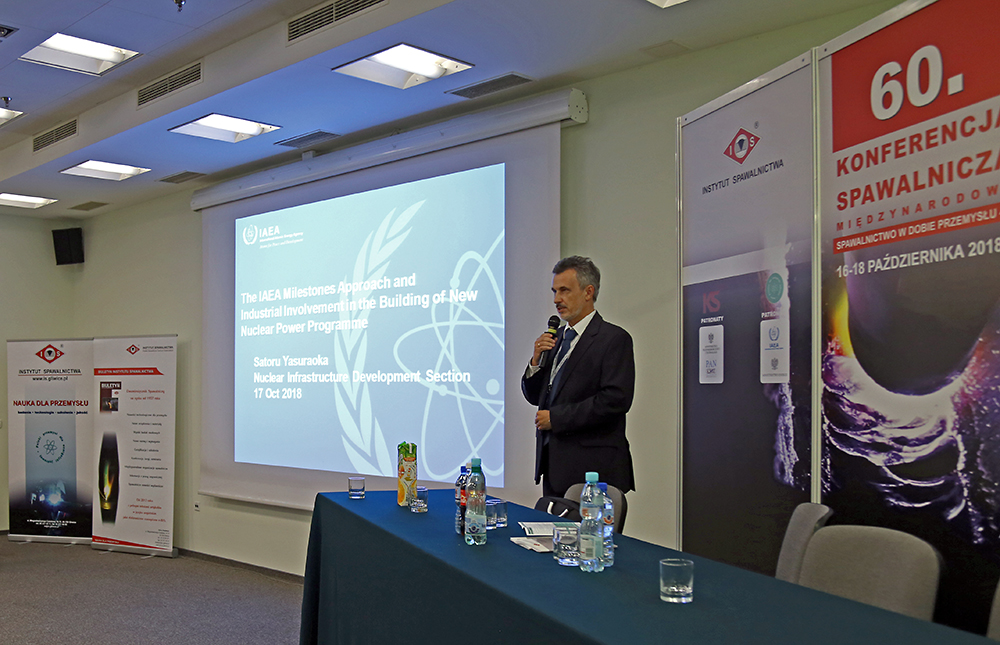
Kolejnym bardzo interesującym wydarzeniem podczas październikowej konferencji była specjalna sesja tematyczna, poświęcona roli spawalnictwa w budowie elektrowni jądrowej, zorganizowana pod hasłem „Łańcuch dostawców konstrukcji spawanych i usług NDT w budowie pierwszej polskiej elektrowni jądrowej”. W czasie tej sesji wygłoszono 6 referatów. Ponadto, 16 i 17 października zostały zorganizowane warsztaty Międzynarodowej Agencji Energii Atomowej (IAEA – International Atomic Energy Agency). Głównym organizatorem sesji był Instytut Spawalnictwa w Gliwicach przy wsparciu i pod patronatem Ministerstwa Energii oraz IAEA. Do udziału w sesji zaproszono również przedstawicieli potencjalnych dostawców technologii jądrowych, tj.: CGN, EDF/FRAMATOME, HITACHI-GE oraz KHNP/KEPCO.
Podsumowania konferencji dokonał dr hab. inż. Jerzy Łabanowski z Politechniki Gdańskiej, który podkreślił aktualność i różnorodność tematyki wygłaszanych referatów. Zwrócił uwagę na liczną reprezentację zagranicznych ośrodków spawalniczych wśród prelegentów, akcentując międzynarodowy charakter konferencji.
We wszystkich sesjach konferencji spawalniczej uczestniczyło łącznie ok. 350 osób: ok. 270 gości z Polski i zagranicy oraz wielu pracowników Instytutu Spawalnictwa. Oprócz zarejestrowanych uczestników w wybranych sesjach wzięli udział studenci uczelni technicznych (Politechnika Śląska, Akademia Górniczo Hutnicza, Politechnika Częstochowska), którzy licznie skorzystali z tej możliwości.
Referaty:
Rosnące tempo zmian technologicznych w produkcji skraca okres przydatności tradycyjnych kwalifikacji. Utrzymanie wysokiego poziomu aktualnie obowiązującego monolitycznego kształcenia zawodowego wymaga dużego wkładu pracy w zakresie jego aktualizacji i przeglądu, zwłaszcza w kontekście międzynarodowym. Czwarta rewolucja przemysłowa przesuwa tradycyjne systemy edukacji do granic ich możliwości i rzuca światło na ich niedociągnięcia. Zapewnienie, że przyszli pracownicy będą zdolni do wyzwań związanych z Przemysłem 4.0 obejmuje kilka aspektów. Pracodawcy i ich pracownicy wymagają odpowiedniego i na wysokim poziomie szkolenia przed rozpoczęciem zatrudnienia, które dostarczy zarówno podstawowej wiedzy inżynierskiej, jak i wiedzy o najnowszych materiałach i procesach. Celem systemu szkolenia EWF jest zapewnienie właściwego i we właściwym czasie kwalifikowania personelu. Sukces firmy wywodzi się z solidnego i zorientowanego na przemysł systemu jakości z szerokim zaangażowaniem różnych zainteresowanych stron, do których należą instytuty spawalnictwa, ośrodki szkoleniowe, jednostki certyfikujące, firmy, wykładowcy i uczestnicy szkoleń. Podejście oparte na współpracy członków EWF i zainteresowanych stron zapewnia zharmonizowane zapewnienie jakości, które z kolei zapewnia wiarygodność międzynarodowych kwalifikacji, dzięki czemu zyskały one zaufanie pracodawców. W artykule przedstawiono, w jaki sposób kwalifikacje międzynarodowe wspierają wdrażanie i wykorzystywanie nowych technologii, umożliwiając wprowadzanie innowacji do produkcji. Ponadto przedstawiono znaczenie zintegrowanego systemu zapewnienia jakości w opracowywaniu i wdrażaniu kwalifikacji zawodowych, które wspierają mobilność i rozwój w zatrudnieniu.
Koncepcja Przemysłu 4.0 stanowi nowe wyzwanie dla przedsiębiorstw, również dla szeroko pojętej branży spawalniczej. Obecnie mamy do czynienia z IV Rewolucją Przemysłową, która rozpoczęła się w roku 2010, i która spowoduje znaczące zmiany nie tylko w zakresie produkcji wyrobów masowych ale również dotknie życia codziennego. Wiele rozwiązań jakie związane są z nową rewolucją przemysłową będzie wpływało na nas przez najbliższe lata. By sprostać nowym wymaganiom, kadra inżynierska będzie musiała ściślej współpracować w zespołach interdyscyplinarnych i w ten sposób wdrażać do praktyki przemysłowej również technologie spawania, zgrzewania lub klejenia. Producenci urządzeń spawalniczych oferują już rozwiązania, które wpisują się w idee Przemysłu 4.0. Czas jedynie pokaże, w jakim kierunku pójdzie rozwój branży spawalniczej. W pracy przedstawiono idee poszczególnych rewolucji przemysłowych, zarys historyczny rozwoju technologii spawania oraz wymagania dla personelu, który będzie wdrażał i korzystał z efektów Przemysłu 4.0. Zaprezentowano również przykładowe rozwiązania związane ze spawalnictwem.
Konstrukcje inżynierskie wykonane z kształtowników o przekroju zamkniętym wykazują znacznie większą stabilność niż konstrukcje wytworzone z profili otwartych. Węzły konstrukcyjne tego rodzaju ustrojów wymagają połączeń spawanych o krzywoliniowej trajektorii usytuowanej w przestrzeni. Spawanie ram i kratownic z profili o przekroju zamkniętym wytwarzanych w małych i średnich przedsiębiorstwach prowadzone jest zazwyczaj w trybie ręcznym, co jest bardzo czasochłonne i kosztowne. Wymaga też personelu o odpowiednich kwalifikacjach. Spawacze muszą dostosowywać się do stale zmieniających się warunków zarówno w odniesieniu do przygotowania złączy, jak i pozycji spawania. Wymaga to intensywnego szkolenia. Zastąpienie zatem spawania ręcznego procesem zmechanizowanym odciążyłoby spawaczy w sposób znaczący.
Przedstawiono problematykę związaną z lutospawaniem łukowym rur ze stali kotłowej 10CrMo9-10 (10H2M) wyłożonych wewnątrz wykładziną miedzianą. Wskazano na możliwości wytwarzania tego rodzaju połączeń przy użyciu konwencjonalnych i innowacyjnych metod spawalniczych. Przedstawiono wyniki badań radiograficznych, metalograficznych oraz mechanicznych (statyczna próba rozciągania i technologiczna próba zginania poprzecznego, pomiary twardości) złączy lutospawanych wykonanych na zrobotyzowanym stanowisku do lutospawania metodą CMT (Cold Metal Transfer).
Omówiono zagadnienia związane z łukiem mikroplazmowym wykorzystywanym w procesach spawania, napawania i przetapiania. Scharakteryzowano istotę działania oraz warunki jarzenia się łuku plazmowego. Podano właściwości oraz zakres zastosowania spawania plazmowego. Zaprezentowano przykłady złączy cienkich elementów spawanych mikroplazmowo. Omówiono na przykładach wykorzystanie łuku mikroplazmowego w procesach napawania oraz przetapiania. Wskazano na korzystne cechy łuku plazmowego oraz jego potencjał aplikacyjny jako alternatywę dla innych spawalniczych źródeł ciepła.
Przeprowadzono badania wpływu jedno- i czterokrotnego oddziaływania cyklu cieplnego spawania naprawczego na własności mechaniczne złączy doczołowych blach o grubości 18 mm ze stali ulepszonej cieplnie gatunku S1100QL. Określono własności mechaniczne złącza produkcyjnego oraz złączy naprawianych z użyciem obróbki mechanicznej, wykonywanych metodą MAG drutem elektrodowym proszkowym o rdzeniu metalicznym (proces 138) gatunku STEIN-MEGAFIL 1100 M. Stwierdzono, że własności mechaniczne złączy naprawianych z użyciem obróbki mechanicznej są zbliżone do odpowiednich własności złączy po spawaniu naprawczym z usuwaniem wadliwej części spoiny za pomocą żłobienia elektropowietrznego.
Podano informacje o nowych materiałach dodatkowych do spawania popularnych gatunków stali nierdzewnych. Omówiono powstawanie Cr6+ w pyle i związek metali alkalicznych z tym procesem. Opracowane zostały elektrody otulone i druty z rdzeniem proszkowym charakteryzujące się zmniejszoną emisją pyłu podczas spawania i mniejszą zawartością kancerogennego chromu sześciowartościowego w pyle. Jedną z głównych trudności, jaką było zapewnienie niezbędnych właściwości otuliny elektrod rozwiązano, stosując otulinę dwuwarstwową. Nowe gatunki elektrod i drutu proszkowego poddano testom, m. in. w brytyjskim TWI, w celu porównania emisji pyłu i zawartości Cr6+ z materiałami standardowymi. Badania wykazały, że emisja Cr6+ u źródła jest 4 razy mniejsza w przypadku elektrod i 3-krotnie mniejsza dla drutów proszkowych, w porównaniu z materiałami standardowymi.
Trwałość zmęczeniowa połączeń spawanych w warunkach zmęczenia średnio i wysokocyklowego była do niedawna jednym z czynników ograniczających szersze zastosowanie stali o wysokiej wytrzymałości. Ostatnie badania nad zwiększeniem trwałości zmęczeniowej złączy spawanych pokazują, że trwałość zmęczeniowa spoin (złączy spawanych) może zostać znacznie zwiększona za pomocą wysokoczęstotliwościowej mechanicznej obróbki udarowej (High Frequency Mechanical Impact -HFMI). Przeprowadzone niezależnie badania wykazały, że wzrost trwałości zmęczeniowej jest proporcjonalny do wytrzymałości materiału rodzimego przy stosowaniu tej metody. Metoda ta opiera się na wprowadzeniu naprężenia ściskającego w punkcie krytycznym przejścia spoiny w materiał rodzimy i jest zaawansowaną wersją metod opracowanych w latach siedemdziesiątych na terytorium ówczesnego Związku Radzieckiego, stosowanych w celu zwiększenia trwałości zmęczeniowej złączy spawanych konstrukcji łodzi podwodnych. Metoda nadaje się do obróbki zarówno spoin czołowych, jak i pachwinowych. Niniejszy artykuł podsumowuje aktualną wiedzę na temat użyteczności i praktycznego zastosowania metody HFMI dla stali konwencjonalnych (o niższych własnościach wytrzymałościowych) i wysokowytrzymałych. Istotnym czynnikiem wpływającym na wzrost zainteresowania metodą HFMI było uwzględnienie tej metody w zaleceniach Międzynarodowego Instytutu Spawalnictwa (MIS) dotyczących obliczeń zmęczeniowych konstrukcji.
Rozpatrzono charakterystyczne cechy formowania połączenia spawanego stopu tytanu (Ti – TiB) wykonanego wiązką elektronów. Zbadano wpływ późniejszej obróbki cieplnej na przemiany strukturalno-fazowe w metalu spoiny i strefie wpływu ciepła. Obróbka cieplna połączeń spawanych prowadzi do rozpadu fazy metastabilnej, rozmieszczenia cząsteczek boru w strukturze i zwiększa jednorodność strukturalną, co przyczynia się do polepszenia własności mechanicznych.
Omówiono technologię napawania dysków rozwłókniarki wełny mineralnej drutem proszkowym metodą MAG, łukiem samoosłonowym oraz łukiem krytym. Podano wyniki badań trwałości dysków w zależności od składu chemicznego napawanej warstwy roboczej.
Aby przejść do kolejnego etapu rozwoju technologii spawalniczych, tj. zastosowania koncepcji Przemysłu 4.0 i „Internetu rzeczy” w spawaniu, konieczne jest zrozumienie i przekazanie niezbędnej wiedzy personelowi spawalniczemu odpowiedzialnemu za rozwój technologii już dzisiaj, by łatwiej było uzyskać niezbędne dane maszynowe w przyszłości. Dlatego konieczne jest rozwijanie i dostosowywanie nowoczesnego sprzętu spawalniczego do potrzeb inteligentnej fabryki oraz gromadzenia i analiz wielu danych, które są istotne dla procesu spawania. W artykule przedstawiono krótki przegląd możliwości i pomysłów, jakie są dostępne już dzisiaj w celu dostosowania obecnych rozwiązań na potrzeby Przemysłu 4.0 w przyszłości.
Proces zgrzewania tarciowego FSW w większości przypadków jest stosowany do łączenia elementów wykonanych z materiałów jednoimiennych. Zasadniczo, do tego rodzaju konstrukcji wykorzystuje się również niewielką prędkość zgrzewania. W artykule przedstawiono wyniki badań dotyczące wysokowydajnego zgrzewania metodą FSW stopu aluminium przerabianego plastycznie, a także określono wpływ warunków zgrzewania na strukturę i własności powstałych złączy. Uzyskane rezultaty wskazują, że otrzymane połączenia cechują się wysoką jakością i nie zawierają niezgodności spawalniczych.
Problematyka oceny stopnia zużycia elektrod do zgrzewania rezystancyjnego punktowego jest istotnym zagadnieniem, mającym znaczący wpływ na jakość połączeń zgrzewanych. W artykule przedstawiono autorskie stanowisko, które zintegrowano poprzez połączenie robota przemysłowego, systemu wizyjnego, kolumnowej ostrzałki do elektrod oraz lampy “Smart Light”. Elementy stanowiska: czujniki i system wizyjny zostały dobrane pod kątem ich wykorzystania w seryjnej produkcji konstrukcji zgrzewanych. Opracowany i zoptymalizowany system pozwala na automatyczną ocenę stopnia zużycia nasadek do zgrzewania rezystancyjnego punktowego, a zaimplementowane i przetestowane algorytmy decyzyjne umożliwiają przeprowadzenie procesu zgrzewania z ciągłą kontrolą jakości nasadek oraz ocenę możliwości ich dalszego ostrzenia w toku procesu produkcyjnego.
W artykule przedstawiono badania określające wpływ czystości gazu formującego na jakość złączy rur z austenitycznej stali nierdzewnej X5CrNi18-10 (1.4301) o wymiarach: ф 50,8 x 1,5 mm, wykonanych metodą spawania orbitalnego TIG bez użycia materiału dodatkowego. W zakresie przeprowadzonych badań wykonano: badania składu chemicznego, badania zawartości ferrytu delta, badania nieniszczące złączy spawanych, w tym badania wizualne wraz z oceną barw nalotowych od strony grani spoiny oraz od strony lica spoiny, badania radiograficzne i metalograficzne, a także badania niszczące złączy spawanych. Ochronę metalurgiczną lica spoiny stanowił gaz osłonowy w postaci argonu o czystości 5.0, którego natężenie przepływu wynosiło 8 dm3/min. Grań powstającej spoiny była początkowo chroniona poprzez zastosowanie gazu formującego w postaci argonu o czystości 5.0, a następnie mieszanek argonu z powietrzem. Przeprowadzone badania wykazały, że wraz ze wzrostem zawartości tlenu szczątkowego w mieszance gazu formującego następuje zmiana barw warstw tlenkowych występujących w obrębie obszaru SWC oraz obszaru grani spoiny. Ze względu na wymagania zawarte w duńskim raporcie 94.34 Instytutu Force Technology oraz amerykańskiej normie ASME BPE-2012, dotyczące barw nalotowych, jedynie złącze o zawartości 4 i 25 ppm tlenu szczątkowego w mieszance gazów formujących mogą być dopuszczone do użytku po uprzednim oczyszczeniu i pasywacji.
Zjawiska i procesy zachodzące podczas spajania są zazwyczaj bardzo złożone i należy je opisywać metodami wielowymiarowymi. W artykule opisano podstawy metodologiczne i wybrane obszary zastosowania rozwiązywania problemów spawalniczych z wykorzystaniem statystycznych metod wielowymiarowych. Przedstawiono przykłady użycia teorii planowania eksperymentu, analizy regresji wielokrotnej, analizy skupień, analizy składowych głównych i analizy regresji logistycznej. Zastosowanie analiz wielowymiarowych daje możliwość matematycznego opisu procesów spajania, co można, po przeprowadzeniu weryfikacji merytorycznej, wykorzystywać do przewidywania ich skutków, a zwłaszcza do prognozowania właściwości i trwałości eksploatacyjnej konstrukcji spawanych.
Radiografia cyfrowa znajduje coraz szersze zastosowanie w badaniach nieniszczących złączy spawanych i odlewów, pozwalając na otrzymanie powtarzalnej metody badań i skrócenia czasu badania do minimum. Jednak by móc otrzymać prawidłowy wynik, należy w procesie badania wyrobów dokonać weryfikacji poziomów jakości zgodnie z normą wyrobu lub specyfikacją klienta. Proces przygotowania badania w przypadku radiografii cyfrowej ma zasadniczy wpływ na wyniki badań, w związku z czym w artykule omówiono procedurę kalibracji systemu do badań, która pozwala na wzrost poziomu wykrywalności i spełnienia stawianych wymagań jakościowych.
Wytwarzanie konstrukcji z użyciem nowoczesnych materiałów i technologii łączenia nierzadko niesie za sobą problemy związane z ich ograniczoną spawalnością. Zdolność do otrzymywania złączy o wymaganych własnościach może być ograniczona m.in. przez skłonność do występowania pęknięć. W pracy dokonano przeglądu sposobów klasyfikacji pęknięć złączy spawanych i lutospawanych opartych na przyczynach i okresie ich powstawania. Jako podstawowy podział pęknięć związanych z produkcją/wytwarzaniem przyjęto pęknięcia gorące, zimne, lamelarne oraz wyżarzeniowe. Zaproponowano rozszerzenie tej klasyfikacji o szczególne przypadki pęknięć występujących w temperaturze wyższej od temperatury otoczenia i niższej od dolnej granicy zakresu kruchości wysokotemperaturowej. W powstałym w ten sposób przedziale temperatury mogą wystąpić pęknięcia spowodowane utratą plastyczności w stanie stałym na skutek wystąpienia kruchości wysokotemperaturowej II rodzaju oraz pęknięcia spowodowane kruchością w obecności ciekłych metali.
Zastosowanie nowoczesnych materiałów konstrukcyjnych niesie za sobą konieczność dostosowania typowych procesów spawalniczych do specjalnych wymagań wynikających z ograniczonej spawalności wykorzystywanych materiałów. Wynika to nierzadko ze złożonego składu chemicznego lub unikatowych właściwości mechanicznych uzyskiwanych w procesach technologicznych wytwarzania stali i stopów. Przykładem takiej stali jest stal o gwarantowanej granicy plastyczności 1300 MPa, gdzie wysoką wytrzymałość uzyskuje się przez dodatek niewielkich ilości pierwiastków węglikotwórczych i złożonych procesów obróbki cieplnej. Powoduje to, że nie tylko wprowadzenie ciepła podczas spawania może spowodować zmniejszenie tych właściwości, ale i wszelkie zabiegi dodatkowe związane z przygotowaniem brzegów do spawania czy proces podgrzewania wstępnego. W badaniach przeprowadzono proces symulowanego podgrzewania wstępnego przy zastosowaniu różnych warunków chłodzenia. Pozwoliło to określić dopuszczalną temperaturę, przy której nie zachodzą istotne zmiany, jak również temperatury krytyczne, powyżej których następuje istotna zmiana właściwości mechanicznych.
Scharakteryzowano podstawowy problem kontroli właściwości złączy wykonanych ze stali AHSS w odniesieniu do konwencjonalnych stali konstrukcyjnych, bazujący na wyznaczaniu czasu stygnięcia t8/5. Zaproponowane rozwiązanie w postaci zastosowania metody elementów skończonych bazuje na dwóch modelach obliczeniowych. Przedstawiono model materiałowy, który uwzględnia właściwości pojedynczych faz metalicznych oraz ich interakcje w trakcie cyklu spawania. Jako drugi, opisano numeryczny model hybrydowego źródła ciepła HPAW (plazma + MAG) składający się z dwóch predefiniowanych w oprogramowaniu Simufact. Welding modeli, adekwatnych do charakterów procesów składowych. Przeprowadzono symulację spawania oraz eksperyment weryfikujący. Wykazano zgodność wyników symulacji i jej wysoką przydatność w zakresie kontroli właściwości analizowanych złączy.
Lasery włóknowe stanowią nowatorskie narzędzie w rękach spawalnika. Nieustanny ich rozwój, a także opracowywane nowe techniki spawania umożliwiają wykonanie zadań technologicznych bardzo trudnych bądź niemożliwych do spełnienia za pomocą konwencjonalnych laserów technologicznych i konwencjonalnych technik spawania, jak np. spawanie precyzyjnych elementów wykonanych z miedzi, materiałów różnoimiennych, a także materiałów w postaci cienkich folii metalowych lub elementów niedokładnie wykonanych czy też niedokładnie zestawionych. W artykule przedstawiono technikę spawania wiązką promieniowania laserowego odchylaną dynamicznie i omówiono jej zalety w zastosowaniu do spawania miedzi i stopów aluminium, a także do łączenia tworzyw sztucznych. Opisano także technikę zintegrowanego monitorowania procesu „inline coherent imaging (ICI)” umożliwiającą poprawę jakości spawanych elementów.
Opisano zalety procesu spawania hybrydowego laser + MAG. Podano korzyści oraz przykłady zastosowania stali o wysokiej granicy plastyczności S960QL. Przedstawiono wyniki badań spawania hybrydowego złączy doczołowych o różnych grubościach ze stali ulepszonych cieplnie o podwyższonej granicy plastyczności 960 MPa zarówno w pozycji PA, jak i PC. Przedstawiono także wyniki badań metalograficznych makro i mikroskopowych uzyskanych złączy.
Wzrost zapotrzebowania na energię elektryczną powoduje konieczność modernizacji i budowy instalacji o coraz większej sprawności. Budowa bloków energetycznych na parametry nadkrytyczne i ultranadkrytyczne wymaga stosowania nowych technologii i nowych materiałów. W pracy przedstawiono dwa przykłady pękania instalacji kotłowych związane z zastosowaniem nowej technologii spawania hybrydowego oraz materiału Alloy 59. Stwierdzono, że stosowanie najnowszych osiągnięć, zarówno technologicznych, jak i materiałowych, jest zasadne pod warunkiem analizy i weryfikacji założeń konstrukcyjnych i warunków eksploatacji.
Przedstawiono badania których celem była ocena wpływu parametrów technologicznych spawania łukowego elektrodą topliwą blach stalowych z powłokami ochronnymi na wielkość emisji pyłu i gazów (CO, NOx). Wyznaczono korelacje pomiędzy metodą spawania, rodzajem powłoki ochronnej, parametrami prądowymi, rodzajem materiału dodatkowego a emisją zanieczyszczeń. Badania prowadzone były dla spawania metodami MAG, CMT, ColdArc oraz AC MIG Pulse blach stalowych z różnymi rodzajami powłok ochronnych antykorozyjnych. Jako materiał dodatkowy zastosowano drut lity w gat. G3Si1 o śr. 1,2 mm oraz drut proszkowy z wypełnieniem metalicznym o oznaczeniu T3T Z M M 1 H15 o śr. 1,2 mm.
Wieloosiowe pozycjonery spawalnicze oraz tory jezdne przeznaczone do zintegrowania z robotem przemysłowym jako ich zewnętrze osie powinny cechować się, oprócz określonej struktury kinematycznej i szerokiego zakresu ruchów, także wysoką sztywnością, przekładającą się na założoną powtarzalność pozycjonowania. Tego typu wymagania stają nierzadko w sprzeczności, stąd opracowanie bezpiecznej i funkcjonalnej konstrukcji wymaga zaawansowanych metod projektowania i weryfikacji. Dochodzenie do ostatecznego rozwiązania nie może być prowadzane wyłącznie w oparciu o intuicję konstruktora, czy kryterium najniższej ceny. Jednym z uznanych sposobów weryfikacji modeli konstrukcyjnych CAD jest zastosowanie analizy wytrzymałościowej MES (metodą elementów skończonych). W artykule przedstawiono efekty prac badawczo – rozwojowych dotyczących budowy i wdrożenia przemysłowego w PPU „ZAP Robotyka” w Ostrowie Wielkopolskim nowych typów maszyn manipulacyjnych – zewnętrznych osi robotów.
Sesja tematyczna:
Łańcuch dostawców konstrukcji spawanych i usług NDT w budowie pierwszej polskiej elektrowni jądrowej – notatka z sesji.
Patronaty:
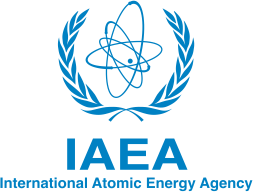
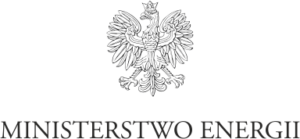
Prezentacje:
- Kamienie milowe oraz zaangażowanie przemysłu wg IAEA w procesie tworzenia nowego programu energetyki jądrowej – Satoru YASURAOKA
- Kompleksowa propozycja współpracy CGN podczas budowy elektrowni jądrowej w Polsce (HPR1000) – Kuang Yanjun, Fan Shubin
- Kontrola połączeń spawanych przed i podczas eksploatacji reaktora EPR – Etienne Martin
- Technologie spawania reaktora ABWR (Potencjalna współpraca z firmami polskimi przy budowie pierwszej elektrowni jądrowej w Polsce) – Yu Kuwada
- Łańcuch dostaw KHNP dla polskich dostawców – Victor Kum
- Wprowadzenie do zagadnień spawalniczych w układach pomocniczych (BOP) elektrowni jądrowej – Gyue-seog Jeong
- Perspektywy udziału krajowego przemysłu spawalniczego w łańcuchu dostaw podczas budowy pierwszej elektrowni jądrowej w Polsce – Jerzy Niagaj
Warsztaty (tylko w j. angielskim) prowadzone przez IAEA z Wiednia
Wdrażanie międzynarodowych kodów, norm i standardów jądrowych do krajowych przepisów technicznych
- The IAEA Milestones Approach and Industrial Involvement to assist developing national nuclear infrastructure – Satoru Yasuraoka
- Industrial Involvement and International codes/standards – technical requirements – Humberto Werdine Viotti
- KEY CONDITIONS for national policies / strategies to allow for a successful industrial involvement – Jean-Marc de Guio
- Nuclear power programme in Poland – Andrzej Sidło
Jak przygotować się do realizacji projektów w sektorze energetyki jądrowej
Sesja posterowa:
- Badania stanu technicznego elementów stalowych w konstrukcjach hydrotechnicznych – Piotr Gotkowski, Robert Jachym
- Badania metalograficzne drutów proszkowych poddanych działaniu środowiska – Aleksandra Świerczyńska, Michał Landowski, Dariusz Fydrych
- Zaawansowane metody projektowania i weryfikacji torów jezdnych i pozycjonerów spawalniczych – zewnętrznych osi robotów – Paweł Cegielski, Dariusz Golański, Paweł Kołodziejczak, Andrzej Kolasa, Damian Rochalski, Tadeusz Sarnowski
- Napawanie wiązką elektronów – analiza procesu – Marek St. Węglowski, Sylwester Błacha
- Charakterystyka mikrostrukturalna materiału deponowanego drutem ze stali odpornej na korozję przy użyciu wiązki elektronów – Łukasz Rogal, Jan Dutkiewicz, Damian Kalita, Marek St. Węglowski, Sylwester Błacha, Robert Jachym
- Zastosowanie wiązki laserowej i elektronów w technologii przyrostowej – własności mechaniczne i budowa mikrostrukturalna – Bogdan Antoszewski, Hubert Danielewski, Marek St. Węglowski, Sylwester Błacha, Robert Jachym
- Influence of heat treatment on the microstructure and mechanical properties of Ti-6Al-4V alloy prepared by 3D printing – Damian Kalita, Łukasz Rogal, Marek St. Węglowski, Jan Dutkiewicz, Tomasz Durejko, Tomasz Czujko
- Spawanie blach stalowych z cynkowymi powłokami ochronnymi a emisja zanieczyszczeń pyłowych i gazowych do środowiska pracy – Jolanta Matusiak, Joanna Wyciślik
- Zgrzewanie tarciowe metodami FSW oraz HSFW wysokowytrzymałych stopów tytanu – Damian Miara, Jolanta Matusiak, Adam Pietras, Maciej Krystian, Marcin Dyner
- Zgrzewanie garbowe śrub i nakrętek z pneumatycznym i elektromechanicznym dociskiem – Zygmunt Mikno, Szymon Kowieski, Adam Pilarczyk, Michał Niemiec