Grupa Badawcza Technologie Zgrzewania i Klejenia oraz Ochrona Środowiska
Grupa Badawcza Technologie Zgrzewania i Klejenia oraz Ochrona Środowiska wchodzi w skład Centrum Spawalnictwa.
Grupa Badawcza Technologie Zgrzewania i Klejenia oraz Ochrona Środowiska prowadzi prace w trzech głównych kierunkach:
- Badania i opracowywanie technologii zgrzewania, w tym zgrzewania tarciowego metodą FSW, szybkoobrotowego HSFW, zgrzewania rezystancyjnego i ultradźwiękowego metali oraz zgrzewania wibracyjnego.
Zakres prowadzonych prac obejmuje zgrzewanie takich materiałów jak:- stopy aluminium,
- magnezu,
- miedzi,
- tytanu
- czy nowoczesnych stali konstrukcyjnych,
- jak również tworzyw sztucznych.
W obszarze zgrzewania tarciowego w ramach projektów opracowana została m.in. głowica do monitorowania parametrów zgrzewania LOWSTIR, ręczne urządzenie do zgrzewania punktowego FSW stosowane w przemyśle motoryzacyjnym, głowica przekładniowa z narzędziem o dwóch różnych prędkościach obrotowych. Opracowano technologie zgrzewania metodą FSW m.in. wysokowytrzymałych stopów tytanu stosowanych na narzędzia chirurgiczne, zgrzewania aluminiowych siłowników bezpieczeństwa, zgrzewania czasz kul zaworów zwrotnych wykonanych z aluminium odlewniczego oraz technologię zgrzewania elementów – wkładek do odlewniczego korpusu silnika. We współpracy z partnerem przemysłowym pracownicy Grupy Badawczej uzyskali patent międzynarodowy dotyczący zastosowania zgrzewania tarciowego do mocowania wkładek w blokach silników spalinowych. W obszarze zgrzewania tarciowego HSFW – High Speed Friction Welding, w ramach projektu INNOMOTO, opracowano i wdrożono kombinowaną technologię zgrzewania elementów elektrozaworów ze stali AISI303, 11SmNPb30 oraz 11SMn3.
Prowadzone są prace badawcze w zakresie zgrzewania rezystancyjnego punktowego, liniowego i garbowego, ze szczególnym uwzględnieniem wymagań materiałowych przemysłu samochodowego. Opracowano warunki technologiczne hybrydowego zgrzewania rezystancyjnego i klejenia dla blach stalowych z grupy AHSS z i bez powłok ochronnych. Badania i opracowywanie technologii klejenia różnych materiałów konstrukcyjnych, ze szczególnym uwzględnieniem stopów aluminium, stali oraz materiałów kompozytowych.
Prowadzone są obecnie próby technologiczne w zakresie określenia wpływu przygotowania powierzchni na wytrzymałość złączy klejowych różnych stopów aluminium, przy zastosowaniu klejów epoksydowych. Dodatkowo w ramach współpracy z Fraunhofer Institute for Manufacturing Technology and Advanced Materials IFAM w Bremen prowadzone są szkolenia dla techników, specjalistów i inżynierów procesów klejenia pozwalające na uzyskanie kompetencji i uprawnień wg wytycznych Europejskiej Federacji Spawalniczej.Badania i opracowywanie warunków i zaleceń dla bezpiecznej pracy przy spawaniu i procesach pokrewnych.
W ramach projektów międzynarodowych, projektu INNOMOTO i krajowych projektów zamawianych dotyczących poprawy bezpieczeństwa i warunków pracy opracowano metodyki i stanowiska badawcze do określania emisji zanieczyszczeń pyłowych i gazowych przy różnych metodach spawania łukowego, laserowego i hybrydowego, lutospawania i zgrzewania rezystancyjnego. Opracowano i obecnie jest rozwijany system doradczy i-EkoSpawanie, który stanowi innowacyjne w kraju narzędzie wspomagające podejmowanie decyzji w aspekcie bezpieczeństwa pracy w procesach produkcyjnych oraz wspomaga obliczenia wielkości emisji do środowiska pracy dla procesów spawania i procesów pokrewnych.
Grupa Badawcza Technologie Zgrzewania i Klejenia oraz Ochrona Środowiska zajmuje się taką tematyką jak:
Instytut oferuje pomoc w rozwiązywaniu problemów oraz opracowywaniu technologii umożliwiających wytwarzanie produktów przy wykorzystaniu:
- zgrzewania rezystancyjnego punktowego, garbowego, doczołowego
- zgrzewania tarciowego, w tym zgrzewania tarciowego z mieszaniem materiału zgrzeiny tzw. FSW (Friction Stir Welding)
- zgrzewania ultradźwiękowego
- lutozgrzewania.
Metoda zgrzewania FSW umożliwia m.in.:
- łączenie blach i płyt aluminiowych, w zależności od wielkości urządzenia, o grubości do 50 mm w jednej operacji, bez gazów osłonowych i bez konieczności ukosowania blach
- zgrzewanie materiałów różniących się właściwościami fizycznymi, np. aluminium z miedzią
- zgrzewanie metali nieżelaznych, w tym metali niespawalnych innymi metodami
- obniżkę kosztów zgrzewania przy równoczesnej wysokiej jakości połączeń.
Obniżka kosztów wynika z nieskomplikowanego sposobu przygotowania blach do zgrzewania, braku materiałów dodatkowych, ograniczenia konieczności stosowania zabezpieczeń niezbędnych przy spawaniu łukowym aluminium i jego stopów.
- zgrzewanie wibracyjne tworzyw sztucznych i innych materiałów konstrukcyjnych,
- zgrzewanie doczołowe gorącą płytą rur do wody i gazu
- zgrzewanie polifuzyjne rur
- zgrzewanie elektrooporowe rur
- spawanie gorącym powietrzem
- spawanie ekstruzyjne.
- badania emisji zanieczyszczeń pyłowych i gazowych dla różnych procesów i materiałów spawalniczych
- optymalizację technologicznych parametrów procesów spawalniczych z punktu widzenia ochrony zdrowia spawacza i środowiska
- badania czynników zagrażających zdrowiu i bezpieczeństwu pracowników oraz środowisku naturalnemu, występujących przy procesach spawalniczych, tj.:
- pyłu całkowitego i respirabilnego
- tlenków azotu i tlenków węgla, ozonu
- substancji kancerogennych
- hałasu słyszalnego i ultradźwiękowego
- opracowywanie koncepcji systemów wentylacji spawalni i stanowisk spawalniczych
- opracowywanie przepisów i wytycznych BHP w spawalnictwie
- konsultacje i porady w zakresie rozpoznawania oraz eliminacji zagrożeń występujących przy spawaniu i cięciu metali.
System doradczy i-EkoSpawanie jest innowacyjnym w kraju narzędziem wspomagającym podejmowanie decyzji w aspekcie bezpieczeństwa pracy w procesach produkcyjnych oraz wspomagającym obliczenia wielkości emisji do środowiska pracy w przypadku spawania i procesów pokrewnych.
System doradczy i-EkoSpawanie oparty jest o bazy danych zawierające wskaźniki emisji zanieczyszczeń pyłowych i gazowych oraz skład chemiczny powstającego pyłu.
Laboratorium Inżynierii Środowiska
Zespół specjalistów Laboratorium Inżynierii Środowiska Łukasiewicz – Górnośląskiego Instytutu Technologicznego, Centrum Spawalnictwa, oferuje szeroki zakres badań i usług na rzecz bezpieczeństwa pracy, ochrony zdrowia człowieka i ekologii w procesach spawalniczych.
Laboratorium Inżynierii Środowiska, wyposażone w nowoczesną aparaturę badawczą, m.in. w automatyczny miernik gazów CO, NOx, miernik hałasu.
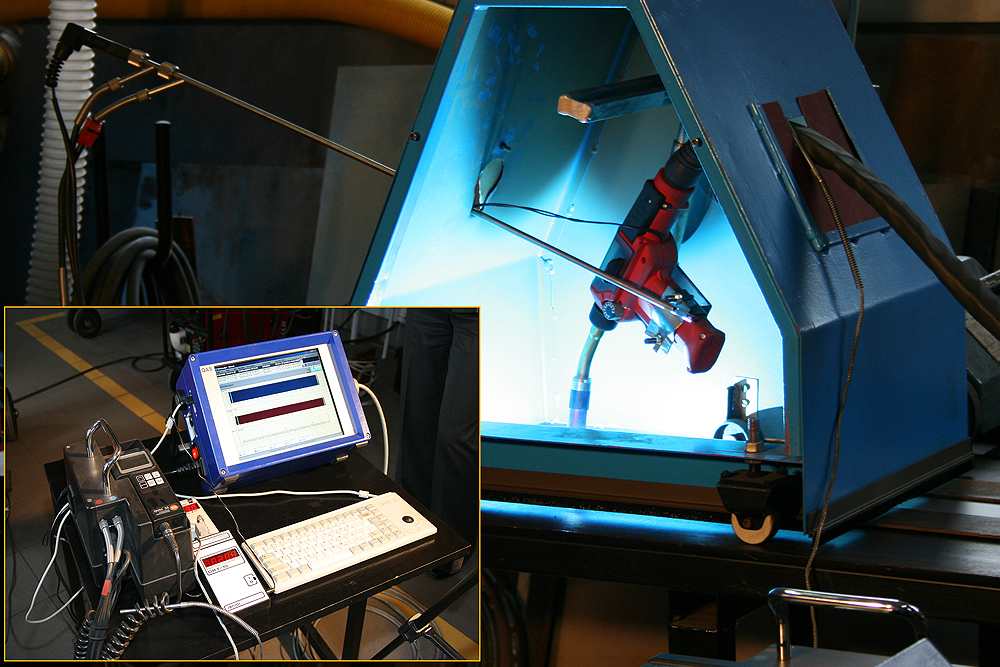
Przykłady oferowanych technologii zgrzewania:
- Zgrzewanie punktowe blach ocynkowanych galwanicznie (<10 µm Zn)
- Zgrzewanie garbowe blach metalizowanych (powłoki Zn, Al, AlSi, itp)
- Zgrzewanie punktowe blach ocynkowanych hutniczo (10÷30 µm Zn)
- Zgrzewanie garbowe prętów na krzyż ze stali niskowęglowych, niskostopowych i stopowych
- Zgrzewanie garbowe nakrętek do blach
- Jednostronne zgrzewanie punktowe cienkich folii stalowych
- Zgrzewanie garbowe elementów okuć budowlanych
- Zgrzewanie konektorów z przewodami w emalii
- Lutozgrzewanie elementów aparatury elektrycznej
- Zgrzewanie punktowe i garbowe tytanu
- Zgrzewanie tarciowe prętów i rur stalowych i z innych metali (np: Cu+Al)
- Zgrzewanie punktowe folii miedzianych < 0,5 mm
- Zgrzewanie garbowe prętów ze stali zbrojeniowych ulepszonych cieplnie metodą TEMPCORE
- Zgrzewanie rezystancyjne złączy Cu + Al o średnicy ø 8÷ ø 20mm
- Zgrzewania mikroelementów na zgrzewarkach inwertorowych
Przykładowe prace badawcze:
W ramach współpracy z firmą Zannini Poland w ramach projektu badawczego w konkursie INNOMOTO, na podstawie licznych badań technologii HSFW, opracowano warunki technologiczne do zgrzewania elementów elektrozaworów wykonanych z dwóch gatunków stali automatowej, tj. 11SMnPb37 i 11SMn37.
Prace badawcze dotyczące możliwości zastosowania zgrzewania HSFW do łączenia elementów elektrozaworów przeprowadzono dla elementów o średnicy 13 mm, wykonanych ze stali automatowych w gatunkach 11SMnPb37 oraz 11SMn37.
Na podstawie prób technologicznych oraz wyników badań sformułowano następujące wnioski:
- technologia zgrzewania tarciowego wysokoobrotowego HSFW jest obecnie najefektywniejszą technologią spajania elementów elektrozaworów wykonanych ze stali automatowej gatunków 11SMnPb37 i 11SMn37, zapewniającą odpowiednie własności użytkowe powstałych złączy;
- wyniki przeprowadzonych badań wskazują, że poprawnie dobrano parametry procesu zgrzewania tarciowego wysokoobrotowego HSFW. Powstałe złącza cechują się wysoką i powtarzalną jakością;
- technologia HSFW jest lepsza do zgrzewania elementów ze stali w gatunku11SMnPb37 niż elementów ze stali 11SMn37. W przypadku złączy ze stali 11SMnPb37 osiągano większe kąty zgięcia podczas prób na zginanie. Wytrzymałości na rozciąganie złączy ze stali 11SMnPb37 oraz 11SMn37 były zbliżone.
Badania wykonano w celu oceny skuteczności i zasadności stosowania metody FSW do wykonywania konstrukcji przemysłowych z ww. stopu aluminium. Przeprowadzono badania wizualne złączy, pomiary temperatury górnej powierzchni złącza FSW w trakcie procesu zgrzewania, badania metalograficzne budowy strukturalnej zgrzein oraz badania wytrzymałości złączy na rozciąganie.
Badania przeprowadzono dla złączy doczołowych wykonanych z płyt płaskich ze stopu aluminium przerabianego plastycznie EN AW-6082 o grubości 6 mm.
Analizując wszystkie badane złącza, wykonane z zastosowaniem różnych prędkości obrotowych oraz prędkości zgrzewania, można wskazać, że parametry te mają wpływ na temperaturę procesu zgrzewania, stopień uplastycznienia łączonych materiałów, a tym samym na strukturę zgrzeiny i kolejno jakość oraz wytrzymałość powstałych złączy. Złącza FSW ze stopu aluminium EN AW-6082, przygotowane w badanym zakresie grubości zgrzewanego materiału, można z powodzeniem stosować w różnych gałęziach przemysłu: lotniczego, kolejowego czy motoryzacyjnego. Jakość powstałych złączy jest wysoka i powtarzalna.
Badania współfinansowano przez Ministerstwo Edukacji i Nauki w ramach grantu nr DWD/4/21/2020
W ramach badań zgrzewano blachy gatunku 22MnB5 AS 60/60 o grubości 1,2 mm po obróbce cieplnej z powłoką AlSi o grubości 10 µm naniesionej dwustronnie metodą zanurzeniową oraz HC340LA z powłoką ZE50/50 Granocoat ZE z obustronną powłoką dwuwarstwową cynkową i z tworzywa sztucznego o grubości 7µm. Do technologicznych prób zgrzewania zastosowano elektrod ISO 5821 – B0 – 16 – 20 – flat – 6 – 30 – A2/2. Próby zgrzewania zostały przeprowadzone na inwertorowej zgrzewarce prądu stałego (1kHz) z pneumatycznym układem dociskowym.
Badania wykazały, że zastosowanie technologii hybrydowej – klejenie + zgrzewanie do łączenia blach stalowych z powłokami ochronnymi powoduje zwiększenie wytrzymałości tych połączeń w porównaniu do połączeń zgrzewanych i klejonych.
Zgrzewanie tarciowe HSFW/FSW elementów elektrozaworów wykonanych ze stali automatowej 11SMnPb37 oraz stali nierdzewnej AlSI304
Badania były prowadzone w ramach projektu pt. „Innowacyjne rozwiązanie technologiczne polegające na kombinowanym połączeniu technologii zgrzewania tarciowego z przemieszaniem (friction stir welding) oraz toczenia na sucho w ramach jednego wielozadaniowego centrum obróbczego o wysokim poziomie równowagi środowiskowej do produkcji elementów elektrozaworów dla branży motoryzacyjnej”.
Celem projektu było opracowanie technologii zgrzewania elementów elektrozaworów w celu zredukowania liczby niezbędnych operacji do ich łączenia, tj. z dwóch odrębnych operacji (stan przed realizacją projektu) do tylko jednej innowacyjnej operacji kombinowanej (stan po realizacji projektu) wykonywanej w całości na jednym wielozadaniowym centrum obróbczym, dzięki któremu możliwe będzie uzyskanie bezpośrednio komponentu cylindrycznego przeznaczonego do produkcji elementów elektrozaworów dla branży motoryzacyjnej.
Na podstawie przeprowadzonych badań stwierdzono, że powstałe złącza cechują się wysoką i powtarzalną jakością. Badania sprawdzające potwierdziły możliwość zastosowania do łączenia elementów elektrozaworów ze stali 11SMnPb37 + stal AlSI304 procesu zgrzewania hybrydowego HSFW/FSW. Potwierdzono również możliwość zastosowania do zgrzewania HSFW/FSW, w celu kształtowania wypływki ze zgrzewania tarciowego wysokoobrotowego narzędzia do FSW.
Łączenie nierozłączne z użyciem techniki zgrzewania jest szeroko stosowane w różnych gałęziach przemysłu, począwszy od produkcji samochodów, przez artykuły gospodarstwa domowego, a na elektronice i łączeniu baterii skończywszy. Komplementarnie z łączeniem konstrukcji stalowych stosuje się technikę klejenia.
Celem badań przeprowadzonych w naszym instytucie było sprawdzenie wpływu warunków zgrzewania oraz klejenia na proces tworzenia połączeń hybrydowych: zgrzewanie rezystancyjne – klejenie materiałów stalowych o podwyższonej wytrzymałości z powłokami ochronnymi.
Łączenie hybrydowe, w porównaniu ze zgrzewaniem, ma liczne korzyści, a są to m.in.: zmniejszenie koncentracji naprężeń w złączu, zwiększenie wytrzymałości połączeń oraz sztywności, poprawa szczelności oraz polepszenie zdolności do tłumienia drgań. Natomiast w porównaniu ze złączami klejowymi, połączenia hybrydowe są bardziej odporne na podwyższoną temperaturę oraz procesy starzenia.
Badania technologiczne obejmowały następujące procesy łączenia:
- zgrzewanie rezystancyjne punktowe blach stalowych w gatunku HC340LA o grubości 1,25 mm z powłoką ochronną dwuwarstwową o grubości 7 μm,
- zgrzewanie rezystancyjne punktowe blach stalowych w gatunku 22MnB5 AS60/60 o grubości 1,2 mm z powłoką ochronną AlSI o grubości 10 μm,
- klejenie z użyciem kleju epoksydowego jednoskładnikowego Betamate 1480v203,
- łączenie hybrydowe: zgrzewanie rezystancyjne punktowe – klejenie blach stalowych w gatunku: HC340LA i 22MnB5, z użyciem kleju Betamate 1480v203, za pomocą techniki weld-through.
Próby zgrzewania przeprowadzono na stanowisku wyposażonym w zgrzewarkę inwertorową typu PMS 14-6MF o częstotliwości 1000 Hz, mocy znamionowej 250 kVA, maksymalnym prądzie zwarcia 50 kA oraz sile docisku elektrod do 1200 daN.
Zbadano możliwość zgrzewania w konfiguracji jednoimiennej blach w gat. HC340LA o grubości 1,25 mm z powłoką ochronną organiczną oraz 22MnB5 o grubości 1,2 mm z powłoką AlSi. Do zgrzewania stali HC340LA zastosowano zgrzewanie z użyciem prostego programu zgrzewania ze stałą siłą docisku oraz jednym impulsem prądowym, natomiast stal 22MnB5 zgrzewano z użyciem programu z dodatkowymi impulsami prądowymi. Badania procesu zgrzewania wykonywano z użyciem elektrod z materiału A2/2 (CuCrZr), wg PN-EN ISO 5182:2009, o średnicy części roboczej 6 mm.
Do klejenia blach stalowych użyto kleju epoksydowego jednoskładnikowego Betamate 1480v203, przeznaczonego do zastosowań w przemyśle samochodowym. Warstwę kleju nakładano na próbki z blachy w następujących stanach przygotowania powierzchni:
- w stanie dostawy – stal HC340LA,
- w stanie po obróbce cieplnej – stal 22MnB5,
- po oczyszczeniu alkoholem izopropylowym – stal HC340LA i 22MnB5
- szorstkowane i trawione kwasem ortofosforowym – stal 22MnB5.
Proces łączenia hybrydowego polegał na naniesieniu na próbki stalowe warstwy kleju epoksydowego jednoskładnikowego Betamate 1480v203, a następnie przeprowadzeniu zgrzewania rezystancyjnego punktowego. Po naniesieniu kleju oraz korekcji wielkości zakładki złącza były zgrzewane, a następnie utwardzane w piecu, w temperaturze 180°C, w czasie 40 min.
Dla zgrzewania złączy hybrydowych czas docisku wstępnego był wydłużany 3-krotnie (do wartości 3000 ms) w stosunku do technologii zgrzewania.
Jakość złączy hybrydowych oceniano na podstawie analizy przebiegu procesu zgrzewania, wyników prób ścinania oraz badań metalograficznych mikroskopowych.
Badania wykazały, że zastosowanie technologii hybrydowej: klejenie + zgrzewanie do łączenia blach stalowych z powłokami ochronnymi powoduje zwiększenie wytrzymałości tych połączeń w porównaniu z połączeniami zgrzewanymi i klejonymi. W przypadku łączenia technologią hybrydową blach ze stali w gatunku 22MnB5 z powłoką AlSi wartość siły ścinania wzrosła o 67% w porównaniu z technologią klejenia, i o 375% w porównaniu ze zgrzewaniem wieloimpulsowym. W przypadku łączenia technologią hybrydową blach ze stali w gatunku HC340LA z powłoką dwuwarstwową organiczną ZE50/50 Granocoat ZE wartość siły ścinania wzrosła o 274% w porównaniu ze zgrzewaniem i o 6% w porównaniu z technologią klejenia. Badania wykazały, że przy klejeniu i przy technologii hybrydowej: klejenie+ zgrzewanie, zastosowanie różnych sposobów przygotowania powierzchni nie wpływa w sposób znaczący na zwiększenie wytrzymałości złączy. W badaniach wytrzymałości złączy klejonych i złączy hybrydowych – klejonych i zgrzewanych blach w gatunku HC340LA, warstwa kleju ulegała zniszczeniu w sposób adhezyjny, czyli najsłabszym miejscem łączenia była powierzchnia przylegania kleju do łączonych materiałów stalowych. Nie następowało oderwanie powłok ochronnych od blach. W badaniach wytrzymałości złączy klejonych oraz złączy klejonych i zgrzewanych blach w gatunku 22MnB5 z powłoką AlSi warstwa kleju miała wyższą wytrzymałość niż siła adhezji powłoki ochronnej do blachy; następowało oddzielenie powłoki ochronnej AlSi od blachy.
Wyniki badań przedstawiono w Biuletynie Instytutu Spawalnictwa Nr 5/2021: Badania warunków technologicznych zgrzewania rezystancyjnego z klejeniem blach stalowych z powłokami – Szymon Kowieski, Jolanta Matusiak